Ceramic lining
WEARTECH uses several types of ceramic linings in its work, namely zirconium alumina, high-alumina ceramics and silicon carbide. Due to their unique properties, these ceramic materials are extensively used to protect industrial equipment from various types of wear. When erosion predominates under existing operating conditions, ceramic materials are most effective. Ceramics have proven absolute resistance to corrosion, both with regard to high-temperature corrosion and to corrosion of the dry and liquid phases of the transported materials.
Assistance and consultation from our experts!
Receive qualified assistance and consultation from our experts. We are ready to answer your questions, tell you about our services and solutions, and also help you make the right decision. Do not hesitate to contact us — we are here to help you!There are many materials for making ceramic linings, each with its own distinctive properties that determine the use of the material in a particular case. WEARTECH effectively uses the following materials to protect production equipment:
Zirconium Corundum
Zirconium corundum (ZrO₂-Al₂O₃) is a high-strength and wear-resistant ceramic that is often used in extreme temperatures and aggressive environments. The main advantages include:
- High thermal resistance: Withstands temperatures up to 1700°C, making it ideal for use in the metallurgical and foundry industries.
- Wear resistance: It has high hardness, which increases the service life of the lining under abrasive wear conditions.
- Chemical resistance: Resistant to corrosion from acids, alkalis, and molten metals.
Alumina Ceramics
Alumina ceramics (Al₂O₃) is one of the most common materials for linings due to its excellent mechanical properties and availability. The main advantages are:
- High hardness and strength: It has exceptional hardness, which increases its resistance to mechanical wear.
- Thermal resistance: Can withstand temperatures up to 1600°C, allowing it to be used in various thermal processes.
- Chemical inertness: Resistant to the effects of most chemical reagents, making it suitable for use in the chemical industry.
Silicon Carbide
Silicon carbide (SiC) is a ceramic material known for its exceptional hardness and thermal conductivity. The main advantages are:
- High thermal conductivity: It has one of the highest thermal conductivities among ceramic materials, contributing to efficient heat dissipation.
- Wear resistance: It has high hardness, resistant to abrasive wear and mechanical damage.
- Corrosion resistance: Resistant to acids and alkalis, as well as molten metals, making it ideal for use in aggressive chemical and metallurgical processes.
Ceramic linings are used in many industries due to their unique properties. Here are some key industries where the use of ceramic linings is appropriate and effective:
Metallurgical Industry
- Furnaces and crucibles: Ceramics are used to line furnaces and crucibles that withstand high temperatures and aggressive environments during metal melting.
- Ladles and molds: Used for lining ladles and molds to minimize heat loss and protect against thermal and mechanical damage.
Mining Industry
- Crushers and mills: Ceramic linings protect equipment from abrasive wear during ore grinding.
- Conveyors and transport systems: Used to line chutes and pipes to extend the service life of equipment and reduce maintenance costs.
Cement Industry
- Rotary kilns and mills: Ceramic linings provide protection against high temperatures and abrasive impact, extending the service life of equipment.
- Heat exchangers: Ceramics help improve heat exchange and reduce wear in heat exchangers.
Chemical Industry
- Reactors and tanks: Ceramics are used to line reactors and tanks that are resistant to aggressive chemical environments.
- Pipelines: Lining pipelines protects them from corrosion and chemical exposure.
Energy Industry
- Boilers and heat exchangers: Ceramic linings are used to protect boilers and heat exchangers from high temperatures and chemical exposure.
- Gas and steam turbines: Used to protect turbine blades from wear and high temperatures.
Glass Industry
- Melting furnaces: Ceramics are used to line melting furnaces, providing protection against high temperatures and the chemical effects of molten glass.
Petrochemical Industry
- Catalytic cracking units: Ceramic linings protect equipment from corrosion and wear at high temperatures.
- Heat exchangers and reactors: Used to protect against aggressive chemical environments and high temperatures.
Food and Pharmaceutical Industries
- Production lines: Ceramic linings are used to protect equipment from wear and chemical exposure during the production process.
These industries demonstrate a wide range of applications for ceramic linings, highlighting their versatility and effectiveness in conditions requiring high thermal resistance, wear resistance, and chemical resistance.
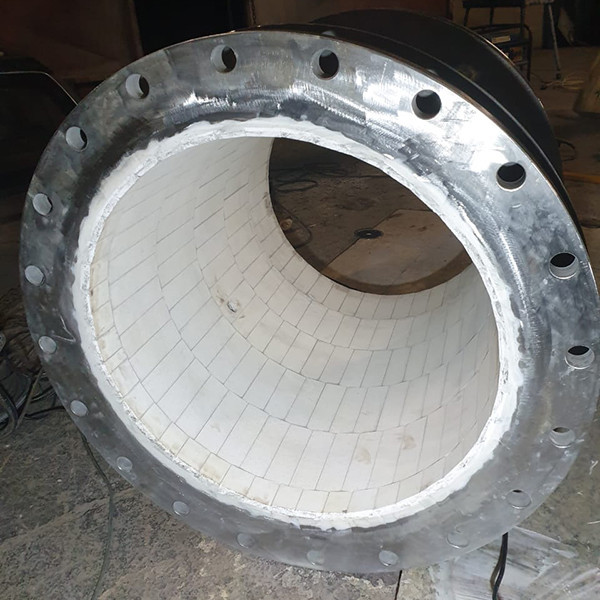
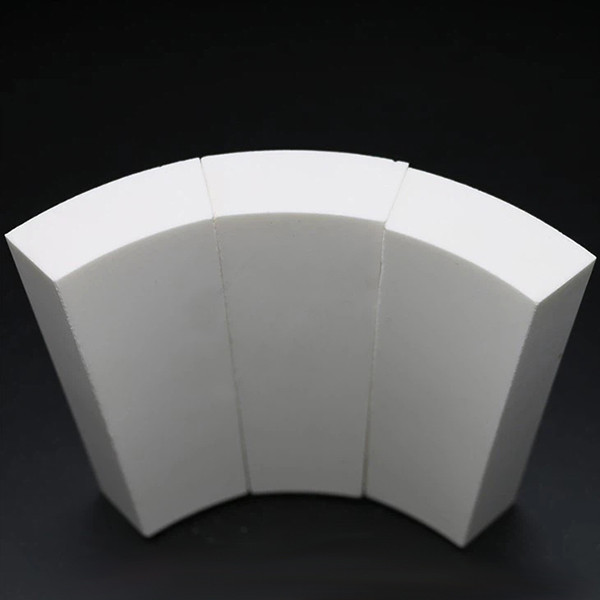
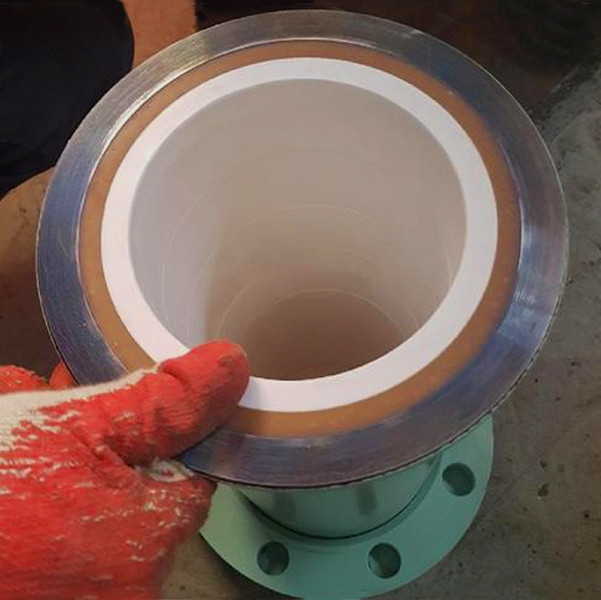
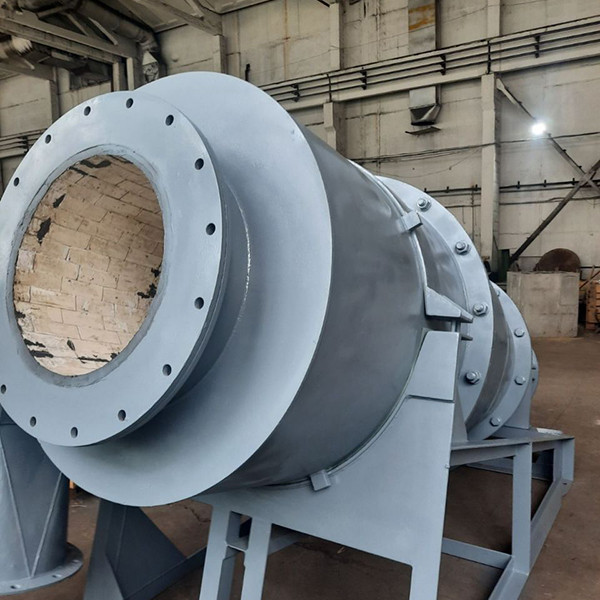
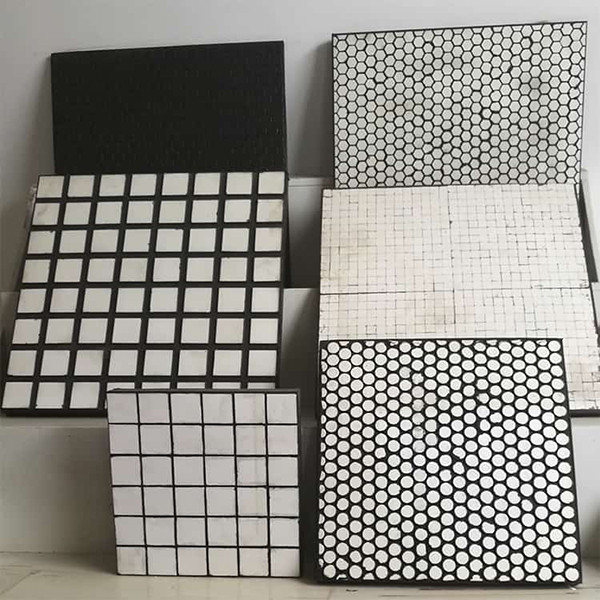
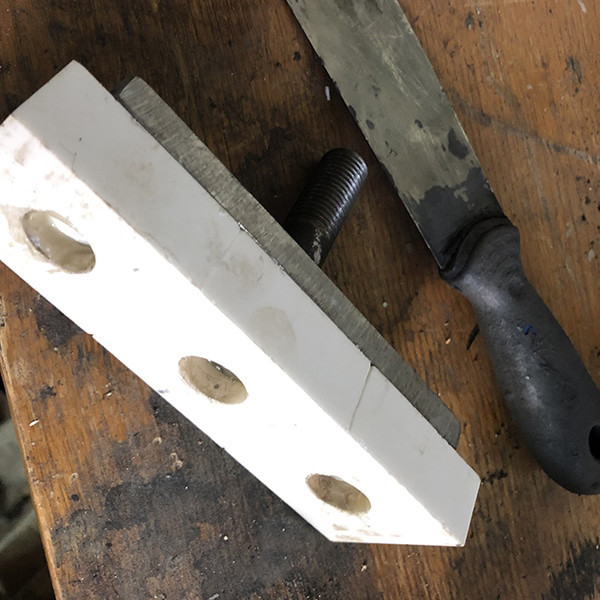
Complete set of ceramic lining
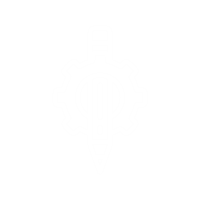
DESIGN
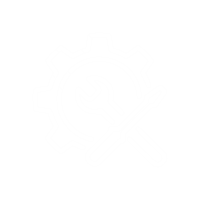
INSTALLATION
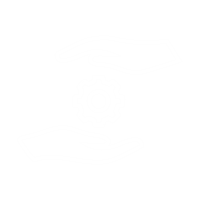
SUPERVISION
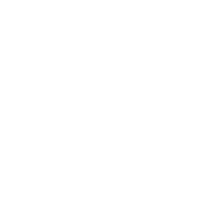
SANATION
Competative Features of Ceramic Lining
- High hardness and wear resistance: Ceramic materials possess extremely high hardness, which ensures resistance to abrasive wear. This extends the service life of equipment under conditions of intensive mechanical impact.
- Heat resistance: Ceramics can withstand high temperatures, making them ideal for use in conditions of extreme temperature exposure, such as metallurgical and foundry processes.
- Chemical resistance: High resistance to corrosion and aggressive chemicals allows the use of ceramic linings in the chemical industry and other environments with high requirements for chemical inertness.
- Low thermal conductivity: Ceramics have low thermal conductivity, which helps to minimize heat transfer and improve thermal insulation of equipment, protecting it from overheating and thermal stress.
- Erosion resistance: Ceramic linings are resistant to erosion caused by high-speed flow of solid particles or liquids, which protects the internal surfaces of equipment.
- Durability and reliability: Due to the combination of all the above properties, ceramic linings significantly increase the service life of equipment, reduce the frequency of repairs, and ensure more stable and reliable operation.
- Mechanical strength: Ceramics have high mechanical strength, allowing them to withstand strong impacts and mechanical loads without damage.
- Cost-effectiveness in the long term: Although initial costs for ceramic linings may be higher, their durability and low maintenance requirements make them economically advantageous in the long term, reducing operating costs and equipment downtime.
These properties make ceramic linings a preferred choice for equipment protection in various industries to provide high efficiency and reliability.
Despite numerous advantages, ceramic linings also have their drawbacks. Here are some of them:
Common Drawbacks of Ceramic Linings
- Brittleness: Ceramics, although possessing high hardness, are brittle materials. They can easily crack or break upon impact or under significant mechanical loads.
- High cost: Initial costs for installing ceramic linings can be high. This is due to the cost of materials and the need for skilled installation.
- Labor-intensive installation: Installing ceramic linings requires specialized knowledge and experience. Errors during installation can lead to material damage and reduced effectiveness.
- Repairability: Repairing ceramic linings can be challenging and costly. In case of damage, replacement often requires large sections, increasing repair time and costs.
- Limited flexibility: Ceramic materials generally have low flexibility. This limits their use in situations where significant deformation or adaptation to changing conditions is required.
- Requirements for operating conditions: Ceramic linings require specific operating conditions. For example, sudden temperature changes can lead to cracks and material damage.
- Weight: Ceramic materials can be heavy, increasing the overall weight of the equipment and potentially requiring additional structural solutions for support.
Nevertheless, ceramic linings remain one of the best solutions for equipment protection in extreme conditions, especially where high thermal resistance and chemical inertness are required. Proper application and installation of ceramic linings can significantly minimize their drawbacks and ensure long-term equipment protection.
WHY WORTH CHOOSING WEARTECH
WE CHALLENGE WEAR & TEAR
OWN PRODUCTION
We produce lining materials
A WIDE RANGE OF PRODUCTS
Different materials - optimum solutions
SELECTION OF THE MOST EFFICIENT SOLUTIONS
Issues are solved on the basis of the best feasibility study
TAILOR-MADE EQUIPMENT
Contact us - we won't let you down
SOLVING NON-STANDARD COMPLEX TASKS
Solving unsolvable tasks is our daily routine!
INDIVIDUAL APPROACH
Our clients become our friends
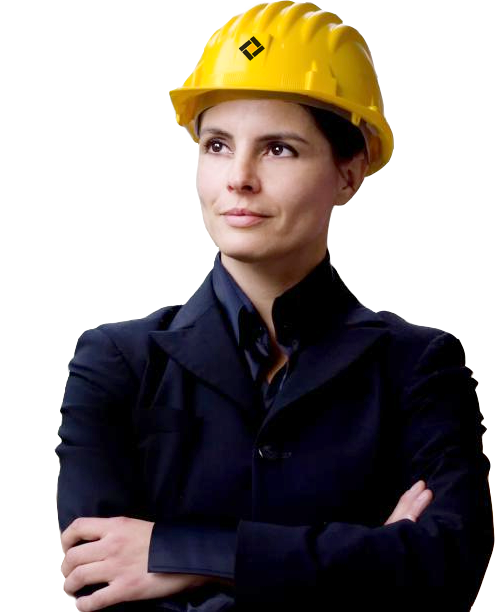