Fused cast basalt
Lining made of cast basalt is an effective solution for protecting equipment under conditions of intense wear and aggressive environment.
Assistance and consultation from our experts!
Receive qualified assistance and consultation from our experts. We are ready to answer your questions, tell you about our services and solutions, and also help you make the right decision. Do not hesitate to contact us — we are here to help you!Cast basalt is an effective lining material due to its unique properties:
- High wear resistance: It has excellent resistance to abrasive wear, significantly extending the service life of equipment.
- Chemical resistance: Cast basalt is resistant to most acids and alkalis, making it ideal for use in aggressive environments.
- Heat resistance: It can withstand high temperatures without losing its properties.
- Low water absorption: This property prevents corrosion and improves durability.
TECHNICAL PARAMETERS | BASALT |
Mohs hardness | Min 8 points |
Specific gravity | 2800-2950 kg/m3 |
Pressure strength | Min 300-450 MPa |
Bending strength | Min 45 MPa |
Abrasion coefficient | Max 0.03 g/cm2 |
Max. operational temperature | 350 °С |
Resistance to temperature fluctuations | before 150 °С, min 50 cycles |
Moisture absorption | 0 |
Acid resistance in sulfuric acid | 0,997 |
Maximum conveying speed | 22 m/s |
Main advantages of the cast basalt lining:
- Durability: Significantly extends the service life of equipment.
- Cost-effectiveness: Reduces repair and replacement costs.
- Versatility: Suitable for use in various aggressive environments.
- Ease of installation: Relatively easy to install compared to other materials.
Cast basalt lining is effectively used in various industries, including the metallurgical industry, mining industry, cement industry, and coal industry (coal-fired power plants and coal preparation plants).
Usage of cast basalt lining in the mining industry
Main types of wear in the mining industry:
- Abrasive wear: Caused by the friction of rocks, ores, and other hard materials against the surface of the equipment.
- Erosive wear: Caused by the flow of particles, which erodes the surface of the equipment.
- Corrosive wear: Chemical effects of aggressive environments (acids, alkalis) leading to the destruction of equipment material.
- Impact wear: Occurs when large chunks of ore or stones fall onto the surface of the equipment.
Technological equipment protected by cast basalt lining:
- Conveyor systems: Used for transporting rocks and ores. The lining prevents wear and extends the life of conveyors.
- Pipes, chutes, and troughs: Used for transporting bulk materials and liquids. Cast basalt protects the inner surface from abrasive and corrosive effects.
- Bunkers and silos: Store and dispense materials. The lining reduces wear on the walls and bottom, improving material flow.
- Mills and crushers: Used for crushing ores. Cast basalt protects the inner surfaces from intense wear.
- Channels and flumes: For transporting slurry and other materials. The lining prevents abrasive and chemical wear.
Key areas in the mining industry where cast basalt lining is effectively used:
- Crushing plants: Protection of the internal surfaces of crushers and mills.
- Transport systems: Conveyors, pipes, and chutes for transporting ores and other materials.
- Scrubbers and thickeners: Equipment for cleaning and thickening ores and waste.
- Dumps and storage facilities: Bunkers and silos for storing bulk materials.
- Flotation plants: Equipment for mineral separation, where lining protects against chemical effects.
Usage of cast basalt lining in the cement industry
Main types of wear in the cement industry:
- Abrasive wear: Caused by the friction of cement materials and clinker against the surface of the equipment.
- Erosive wear: Caused by the flow of particles, which erodes the surface of the equipment.
- Corrosive wear: Chemical effects of cement components and additives leading to the destruction of equipment material.
- Thermal wear: High temperatures in firing and cooling processes can cause thermal destruction of equipment.
Technological equipment protected by cast basalt lining:
- Pipelines and air ducts: Used for transporting cement materials and dust. Cast basalt protects the inner surfaces from abrasive wear.
- Mills: Used for grinding raw materials and clinker. The lining protects against intense abrasive effects.
- Cyclones and separators: Equipment for separating particles by size and density. Cast basalt increases the lifespan of internal components.
- Bunkers and silos: For storing and dispensing cement materials. The lining reduces wear on the walls and bottom.
- Conveyors and troughs: Transport raw materials and finished products. Cast basalt provides protection against abrasive effects.
Key areas in the cement industry for the effective use of cast basalt lining:
- Grinding plants: Mills and crushers, where intensive grinding of raw materials and clinker occurs.
- Transport systems: Conveyors, pipes, and troughs used for moving cement materials at different stages of production.
- Dust collection systems: Cyclones, separators, and filters, where intensive movement of abrasive particles occurs.
- Storage facilities: Bunkers and silos for storing cement materials, which are subject to abrasive wear and erosion.
- Furnaces and heat exchangers: Equipment exposed to thermal and abrasive wear, where cast basalt provides additional protection.
Cast basalt lining is an effective solution for protecting equipment in the cement industry due to its high wear resistance and durability. It is particularly useful in areas with intense abrasive impacts and high temperatures.
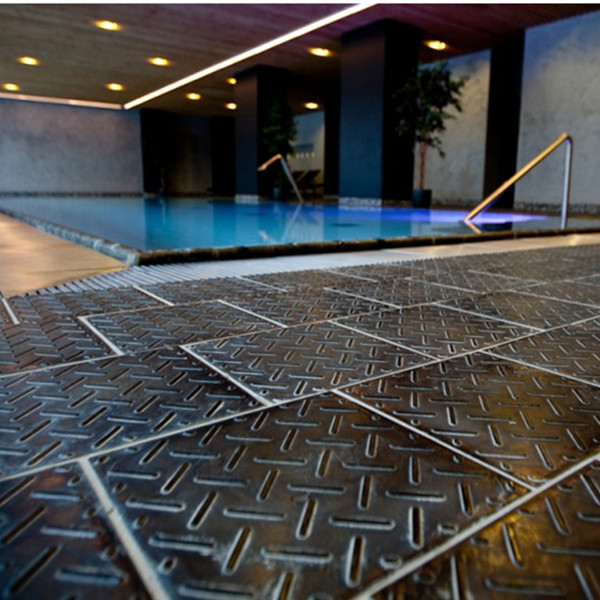
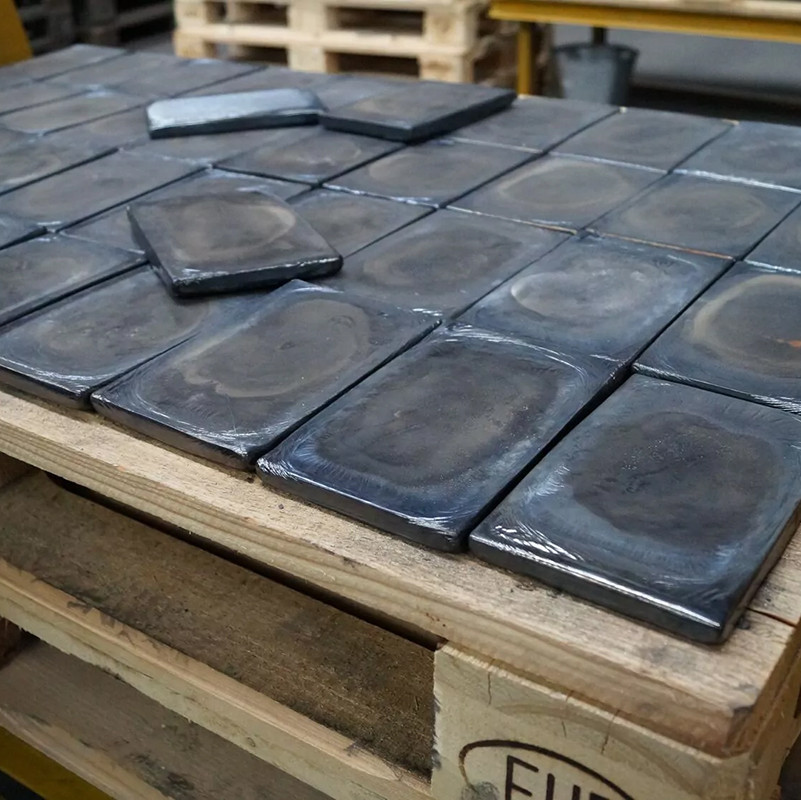
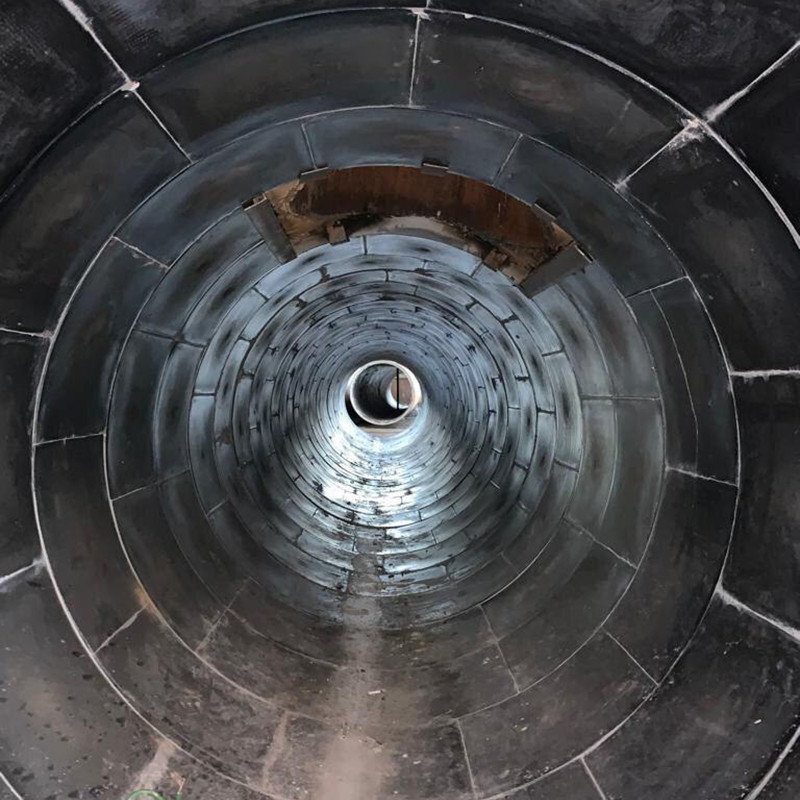
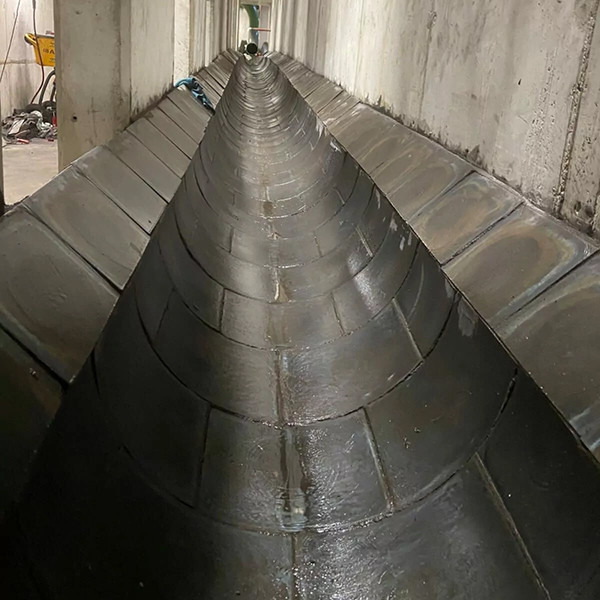
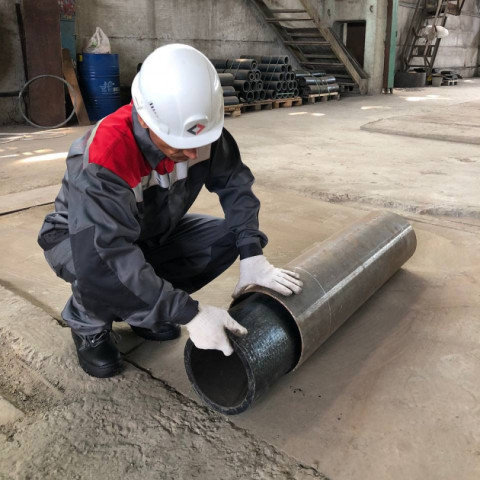
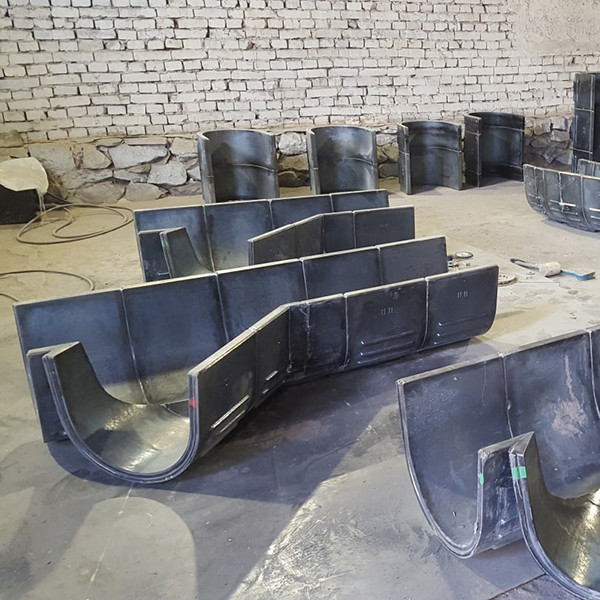
Complete set of cast basalt liners
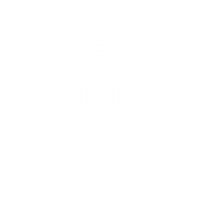
DESIGN
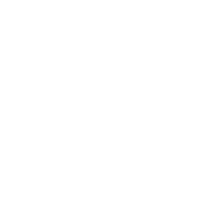
INSTALLATION
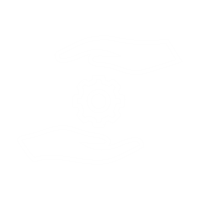
SUPERVISION
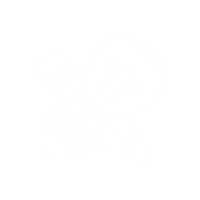
SANATION
Usage of cast basalt lining in the coal industry
Main types of wear in the coal industry:
- Abrasive wear: Wear of equipment due to friction from coal dust and chunks of coal.
- Erosive wear: Surface degradation from the flow of coal dust and particles.
- Corrosive wear: Chemical effects from coal and its combustion products, especially sulfur compounds.
- Impact wear: Damage to equipment from falling large chunks of coal.
Technological equipment protected by cast basalt lining:
- Conveyors and transport systems: Used for moving coal. Cast basalt protects surfaces from abrasive wear.
- Pipes and chutes: Used for transporting coal dust and chunks of coal. The lining prevents wear and corrosion.
- Bunkers and silos: Store coal and feed it for processing and combustion. Cast basalt reduces wear on walls and the bottom.
- Mills and crushers: Used for grinding coal before combustion. The lining protects against intense abrasive effects.
- Cyclones and separators: Equipment for cleaning coal dust and separating particles. Cast basalt increases the lifespan of internal components.
Key areas in the coal industry for effective use of cast basalt lining:
Coal preparation plants
- Grinding systems: Mills and crushers where coal is ground to the required fraction.
- Transport systems: Conveyors and chutes for moving coal and coal dust.
- Storage facilities: Bunkers and silos for temporary storage of coal before processing.
- Dust collection systems: Cyclones and filters for removing coal dust from airflows.
- Washing plants: Equipment for washing coal, where the lining protects against abrasive and chemical wear.
Coal-fired power plants
- Coal transportation: Conveyors and pipes for feeding coal to boilers.
- Pipes and air ducts: For transporting coal dust and combustion products.
- Boilers and furnaces: Equipment exposed to high temperatures and abrasive wear from coal dust.
- Ash and slag removal: Systems for removing combustion products, where the lining reduces wear and corrosion.
Cast basalt lining is an effective solution for protecting equipment in the coal industry, especially in coal preparation plants and coal-fired power plants. Its high wear resistance and durability make it ideal for conditions of intense abrasive and chemical exposure.
In conclusion, cast basalt lining is excellent for conditions with high abrasiveness and chemical exposure. In general, the choice of lining material depends on the specific operating conditions and equipment requirements. A combined approach is often used at production facilities, where the most suitable materials are selected for different areas, including alumina ceramic and bimetallic linings, as well as other recognized effective materials.
WHY WORTH CHOOSING WEARTECH
WE CHALLENGE WEAR & TEAR
OWN PRODUCTION
We produce lining materials
A WIDE RANGE OF PRODUCTS
Different materials - optimum solutions
SELECTION OF THE MOST EFFICIENT SOLUTIONS
Issues are solved on the basis of the best feasibility study
TAILOR-MADE EQUIPMENT
Contact us - we won't let you down
SOLVING NON-STANDARD COMPLEX TASKS
Solving unsolvable tasks is our daily routine!
INDIVIDUAL APPROACH
Our clients become our friends
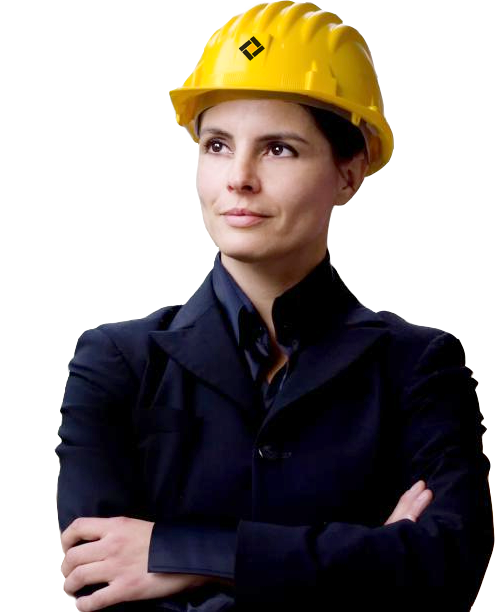